Maintenance: more than you expect
In manufacturing plants for technology markets, cleanliness, efficiency, precision and safety are of crucial importance. There's no room for error. It is therefore not enough to plan, build and equip a state-of-the-art production facility. It also needs maintenance to ensure it always works as designed. The systems require constant attention and preventive maintenance. Regular inspections are just as necessary as software updates.
At KINETICS, we know what it takes to stay ahead in the fast-moving and highly specialized world of microelectronics, biopharmaceuticals, data centers and research and development. For more than four decades we have been responsible for state-of-the-art production facilities in all regions of the world.
Thanks to our many years of experience, we have knowledge of almost all tools and components that are used in our target industries that is unique on the market. This is also reflected in the quality of our maintenance services. We perform system upgrades, supply and install spare parts, and help our customers keep all chemical and gas systems, CDA compressors and dryers operating at optimum efficiency.
Our maintenance programs optimize safety performance, reduce total cost of ownership, improve equipment uptime, and increase the quality and consistency of process media.
Plant maintenance activities:
- Preventive maintenance
- Inspection of facilities and equipment
- Replacement of filters
- Repair and replacement of pumps
- Maintenance and calibration of the gas detection system
- Inspection of electrical distribution panels and control modules
- Maintenance of surveillance systems
- Measurement and analysis
- Documentation procedures & QA/QC
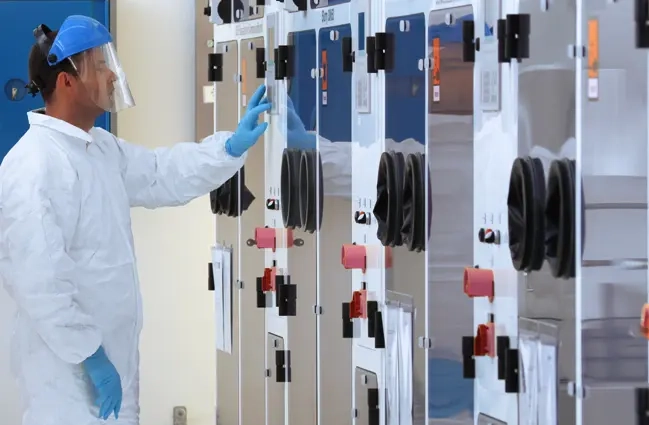
Predictive maintenance: prevention instead of repair.
Preventive maintenance (or English predictive maintenance) serves to identify an imminent failure of equipment and to initiate preventive measures to prevent it. This includes four pillars:
- data collection,
- data transfer,
- data analysis and
- measures.
After the test or maintenance, the recorded data is digitally transferred to a corresponding system, where it can be evaluated from various points of view. In the event of imminent problems, the necessary measures can then be initiated in good time to prevent a failure or a longer downtime of the system.